There are very few buildings in the world that can be described as “sailboat-shaped.” The recently opened Olympia has added one to Brooklyn’s Dumbo neighborhood, inspired by the area’s maritime and industrial history.
The 33-story residential tower is located next to the anchorings of the Brooklyn Bridge with views of Manhattan across the East River.
Developed by Brooklyn, New York-based Fortis Property Group and designed by New York City-based Hill West Architects, with construction management by New York City-based Urban Atelier Group, the Olympia includes 76 luxury condos and 38,000 square feet of indoor and outdoor amenities. The structure’s bottom floors stretch out in a long, tapered shape that resembles the deck of a ship, while the upper floors form a sail shape with an angled silhouette that grows more dramatic near the top of the tower.
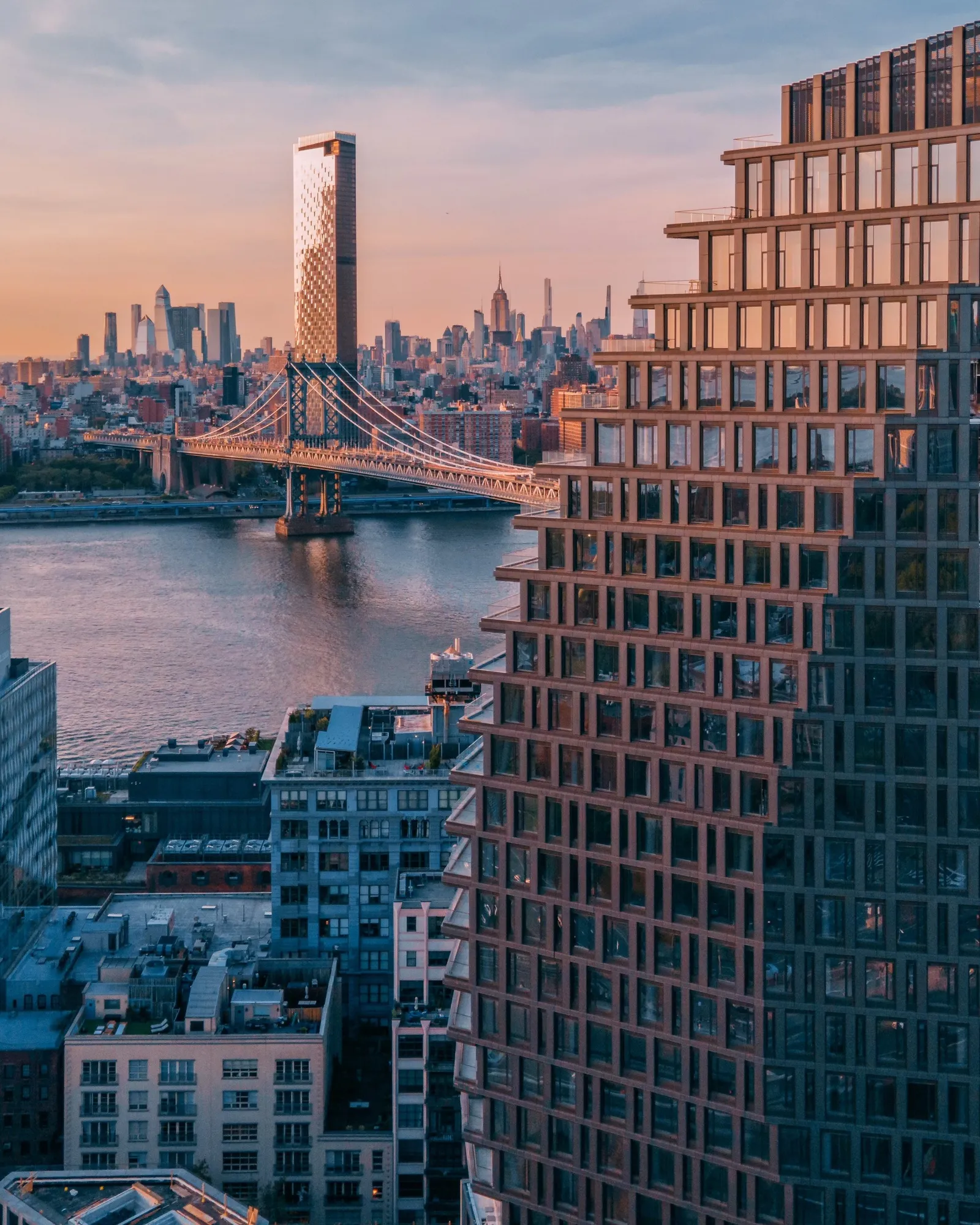
Olympia’s condos range from one to five-plus bedrooms with prices starting at $1.5 million, according to the property website. Because of the building’s curved shape, every one of the floors has a different layout, but common features include open concept kitchens and terraces that span the full length of the living area, forming the edge of the building’s “sail.”
Amenities include a private landscaped garden, an indoor pool and sauna, a playground and water park, an outdoor lounge, a fitness center and a two-lane bowling alley.
While the end result is striking, the building’s structure required a number of unique construction considerations. On top of this, most construction work took place during the peak of the COVID-19 pandemic — forcing the construction management team to adjust on the fly to new challenges and restrictions related to health and safety.
Here, Andy D’Amico, founding president and CEO of UAG, spoke to Multifamily Dive about the construction process, the complexities of the building’s design and the challenges of building during the early days of the pandemic.
This interview has been edited for brevity and clarity.
MULTIFAMILY DIVE: What were some of the challenges you faced in creating such a unique building?
ANDY D’AMICO: From a design perspective, the building's unique structure, twisting and turning within its shell,
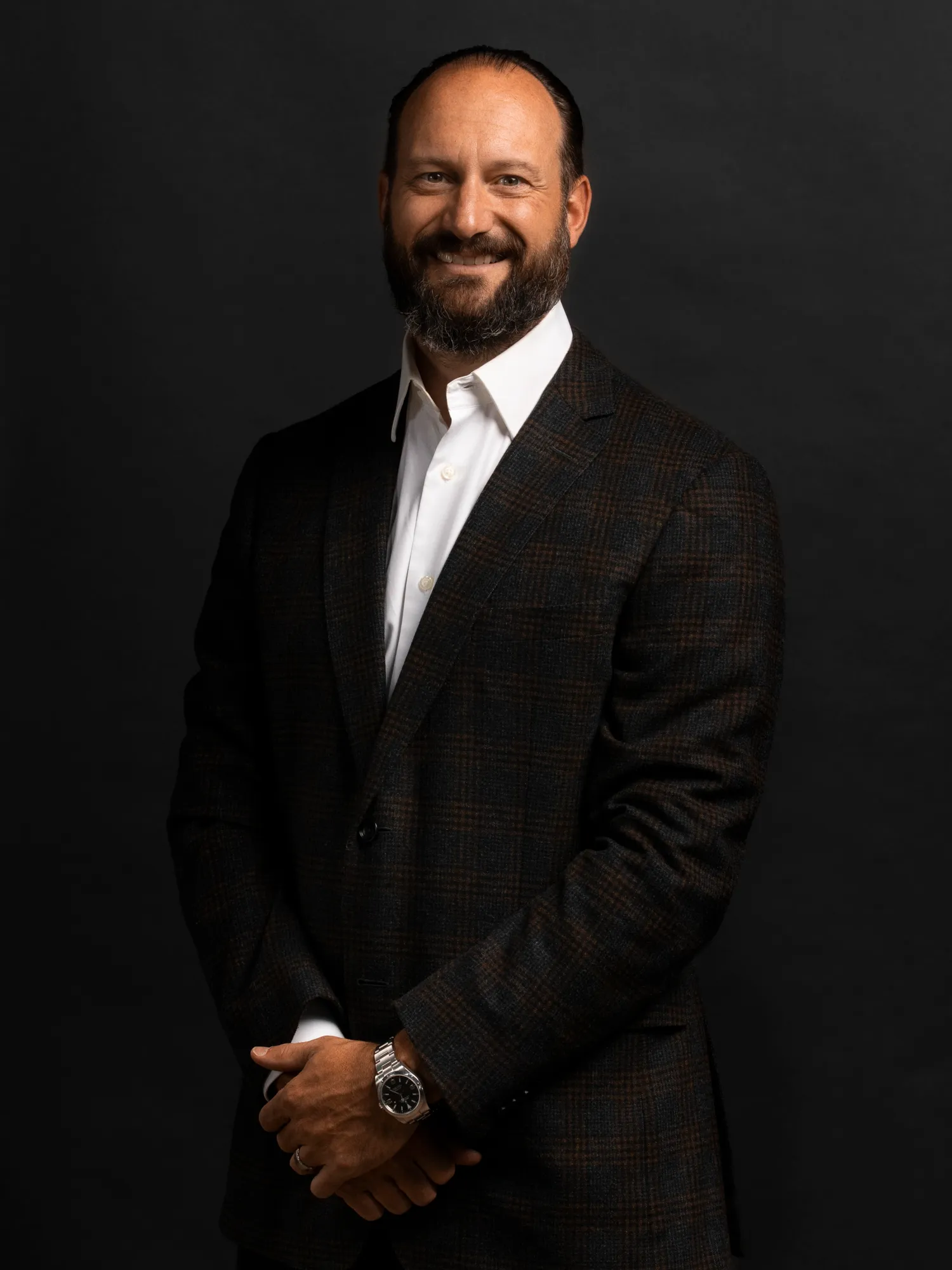
resulted in varying floor plates that necessitated a creative approach to construction. The building's setbacks and terraces also resulted in atypical slab edges, requiring extensive surveying, coordination and enhanced safety initiatives to ensure changes in concrete, window wall and interior tolerances were accounted for and meticulously constructed.
The project team relied on collaborative preplanning to safeguard the trade constructors while protecting the construction completed below.
What are the advantages and disadvantages of this building’s unconventional footprint and design?
The individuality of the residential layouts attracts potential buyers and sets the development apart architecturally.
Considering the unique location in historic Dumbo, the tower's zoning requirements, adjacent neighboring structures and its site positioning set back off the podium on which it rests, the hoist and crane locations were critical. UAG strategically positioned the hoist through the podium level to streamline workflow and general processes.
Logistically, UAG could not utilize a tower crane to reach the top of the building, which required the use of both mobile and spider cranes. Despite this challenge, UAG was a liaison between key stakeholders and maintained constant communication to ensure the construction met the original design intent.
What were some of the obstacles that the COVID-19 pandemic posed to the development and construction of this project?
Beyond design and construction, the development required a far more agile approach to maintain the project team's continued health and standard on-site safety precautions.
UAG navigated newly imposed social distancing measures while remaining cognizant of site logistics, overcoming an industry-wide learning curve to develop a series of internal operational best practices. Additionally, due to uncertainty in the marketplace, supply chain and material sourcing posed challenges for the broader industry.
As a result, the team pivoted to meet critical project milestones, sourcing materials from various locations within the United States and abroad. These practices served to minimize the effects of the pandemic.